lithium-ion batteries for vertiv ups systems
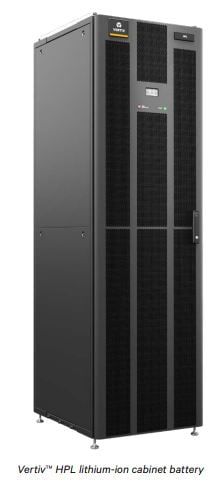
In today’s UPS System wide application universe. Applications for traditional VRLA (Valve Regulated Lead Acid) battery systems, as well new high technology Lithium-Ion Systems range across all industries. There are benefits to both. VRLA will still provide a mainstay place in application for years to come. While Lithium-Ion Battery Storage for UPS Systems will provide large benefits to the marketplace in general.
A Scalable Storage Solution for Dynamic Demands
Measuring up Lithium-Ion Batteries for UPS Systems and Use
Footprint
More power packed into a compact footprint. In a data center or critical operations setting space is always at a premium. A lithium-Ion battery system will provide anywhere from 50%-70% space saving vs other traditional battery system or VRLA footprints.
Life of Battery
Depending on the technology and size, the average life of a lithium-ion battery can be 10-15 years. Compared to a VRLA battery which is 3-5 years. The difference in performance is considerable. The cap ex planning events surrounding VRLA systems or much more frequent.
Maintenance Requirements
Lithium-ion battery systems are low maintenance. They rely on real-time monitoring systems (which add cost), however the required semi-annual or quarterly physical maintenance checks are not required like VRLA batteries do. Overall the added capital expenditure on the front end of purchase tends to outweigh the longer term maintenance costs over 10-15 years.
Runtime Differences
The difference between VRLA and Lithium-ion battery runtime performance is not a linear relationship. VRLA batteries are much better at providing longer runtime scenarios as of now. Lithium-ion batteries can achieve efficient short spurts of power storage. With additional strings provide mid-range runtime performance. You will find certain model UPS units and specific runtimes available with Lithium-Ion batteries.
Heat Rejection
Lithium-Ion Batteries provide minimal heat rejection compared a traditional UPS battery or VRLA battery. Ventilation requirements are greatly reduced. BTU requirements affecting local HVAC sizing are greatly reduced. I addition to heat rejection, ventilation requirements are greatly reduced, and need for certain fire code initiatives, (see local codes).
Cost Comparison
Cost comparison of lithium-ion vs. VRLA do vary greatly, and the gap is closing. These costs depend greatly on the size of system. Whereas lithium-ion battery systems when first introduced were 2-2.5 times the cost of VRLA. They have closed the gap and can be found to be 1.3-1.8 times the costs currently.
How do Lithium-Ion UPS Batteries Work?
In a standard Lithium-Ion Battery System there are three components.
- That Battery Module (BM)
- The String Management System (SMU)
- The Battery Module BMS (BMS)
- Rack BMS
The total battery cabinet chassis provides space for the lithium-ion Battery Modules, the String Management Unit (SMU), and the Battery Module BMS (BMS), plus interconnection wiring and communications cabling.
Battery Module (BM) Disclosures
The Battery Module (BM) contains the Lithium-Ion energy storage.
There is a Battery Module BMS (BMS) inside every battery module. The battery module is an interchangeable component and can be replaced or serviced individually.
Battery Module Sensors (BMS)
The Module BMS located inside the Battery Module will continuously check the temperature and voltage of the individual battery module. The Module BMS constantly sends data to the String Management Unit (SMU) data regarding that module. The SMU receives all the battery module data and can then send commands back to the module to control cell balancing and performance.
String Management Unit (SMU)
The SMU will receive and compile all the data received from the BMS in each battery module. The SMU can control each battery module individually. The SMU “state of charge” measurement can control rate of charge power to each individual battery module. The SMU “state-of-health) also provides key data as to the comparable health of one battery module over the other.
Rack BMS
The rack BMS receives all data from individual Battery BMS units and is the main controller. The rack BMS provides communications between the battery module BMS and the main cabinet circuit breaker plus shunt control.
single source ups provider
Expert assistance from Technical Consultants assist in the selection process of your next UPS System.
Our team is available for Technical Review of specifications, Sizing assistance, Voltage selection, and Runtime Calculations.
Latest News
Stay up-to-date with Vertiv UPS Systems' news and resources about the industry!
Contact Us
Request a Quote from a Product Specialist
Experienced Product Representatives are on hand to send you information and quotations for equipment. If you need help with sizing, installation planning, or general questions about products, please fill in the appropriate form below and someone will contact you shortly.
You may also call 844-501-1887 to get a direct product representative. Or you may chat with one of our product specialists in the chat box provided.